Disclaimer: This blog offers broad insights and does not constitute specialised legal, financial, or compliance advice. Always consult local HR or legal experts for counsel aligned with your region’s labour rules and your unique SMB situation. (References: Guidance on tackling subpar employee performance, Recognised frameworks for resolving underperformance challenges, Workplace motivation research, Recommendations for proactive interventions, Mental health considerations, Strategies for mitigating underperformance in the workplace, Practical methods to prevent performance declines, Upskilling benefits to remain competitive, Analysis of root causes behind staff productivity gaps, Expert advice on avoiding stagnation at work. Consult HR or legal professionals for local compliance and strategy specifics.)
Table of Contents
- 1. Got high stakes? Let’s talk rosters
- 2. Tripped up by costly pitfalls?
- 3. Three keys to shift success
- 4. Spreadsheets or smart tools?
- 5. Your RosterElf roadmap
- 6. Stories and wins you’ll love
- 7. Rules, records, and Aussie realities
- 8. Measure, improve, repeat
- 9. Conquer real-world obstacles
- 10. What’s next? AI, wearables, and more
- 11. Why this edge matters
- 12. Reinvent shifts with RosterElf
1. Got high stakes? Let’s talk rosters
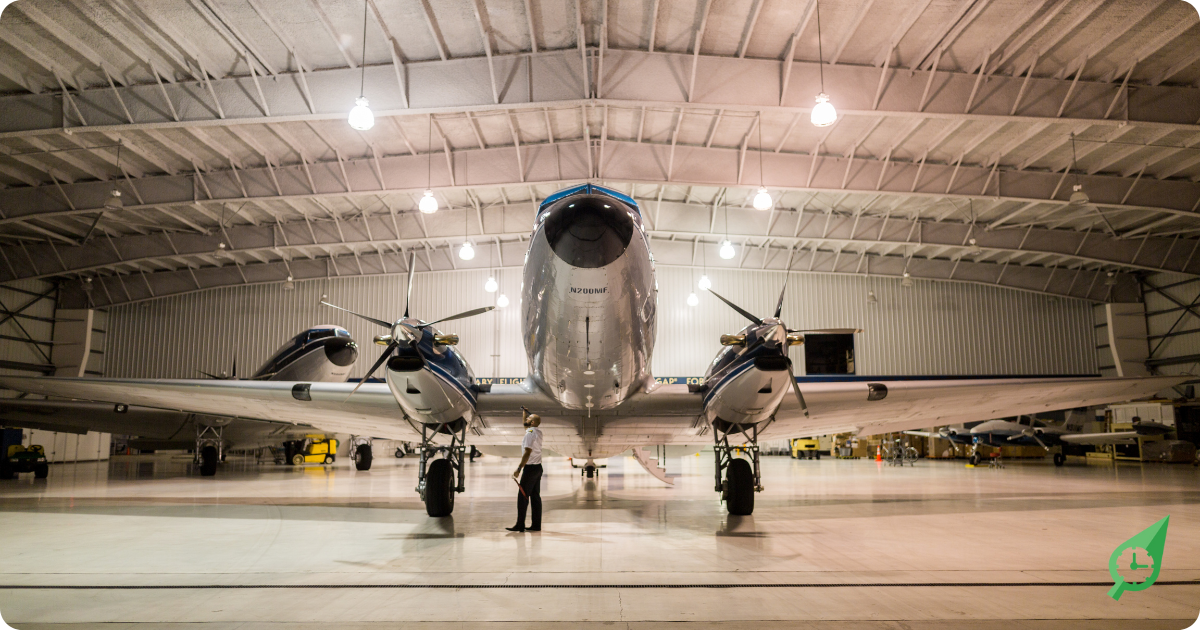
1.1. A single slip causes chaos
In aerospace, a minor misallocation—like having an unqualified operator run crucial tasks—can unravel workflows, spark rework, or annoy clients. Aussie SMEs often eye locally proven roster platforms or tools linking with Xero systems to keep staff assignments precise.
1.2. Even small shops face big rules
Smaller enterprises still confront strict Civil Aviation Safety Authority and AS9100 guidelines. Overlooking a licence or training renewal might shorten corners but endangers safety. A modern scheduling approach that ties credentials to each shift ensures no one lands a task they can’t handle.
Opinion: A minor workshop can’t risk messy rosters in a domain with zero tolerance for slip-ups.
1.3. Balancing image and reality
Clients judge reliability by timeliness and minimal defects. Yet smaller shops juggle labour oversight alongside engineering or procurement duties. A single flawed roster can overshadow robust production strategies. Tools built for friendly Aussie-SME UIs or user-friendly yet powerful apps help keep your scheduling consistent, vital in a world where late shipments can echo long term.
2. Tripped up by costly pitfalls?
2.1. Surprise overtime drains profits
A flimsy roster structure means late coverage calls, spiking unbudgeted hours. In an exacting sector with frequent checks, these costs pile up. Employee-centric schedulers that curb labour overheads are a wise safeguard.
Overtime impact vs. scheduling solutions
Method | Overtime Risk | Admin Load | Staff Morale |
---|---|---|---|
Manual (whiteboard) | High—last-minute fill-ins | Medium—updates often missed | Low–moderate—staff see confusion |
Basic app | Moderate—partial checks | Medium—better than manual | Moderate—some structure, not complete |
RosterElf | Low—auto matching, fewer gaps | Low—skills & compliance built | High—predictable, staff trust schedule |
2.2. Slips in quality control
Overworked or underqualified staff on advanced operations can breed quality defects. In an industry craving near-flawless results, that’s catastrophic. Tools that tie tasks to right skill sets ward off these slip-ups, protecting your QMS reputation.
2.3. Morale plunges on shaky schedules
Erratic, last-minute rosters crush staff faith, especially in smaller crews. Forced overtime drains passion for detail-oriented tasks. A system that slashes admin duplication and cuts idle hours shows respect for their time, crucial for retaining specialists in a competitive sector.
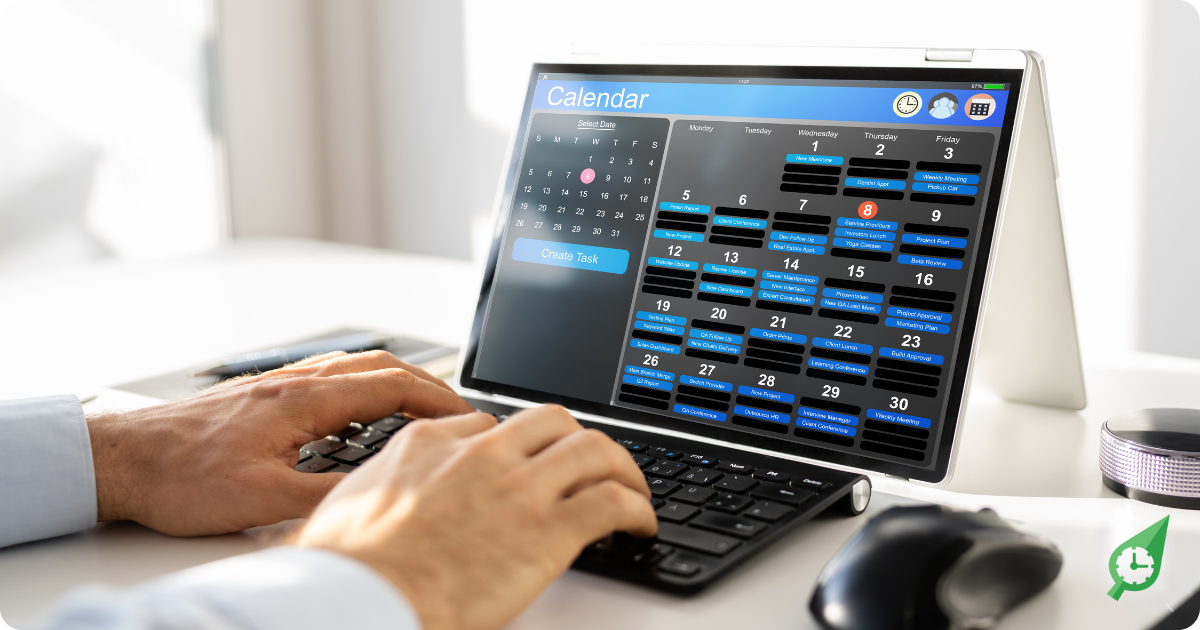
3. Three keys to shift success
3.1. Plan by real demand
Use factual data—assembly deadlines, known supply arrivals—to form rosters. Otherwise, you’ll juggle empty lines in quiet spells and forced coverage in spikes. A roster guide for Australian norms helps incorporate local constraints like union rules.
3.2. Cultivate multi-skilled operators
If a single technician is the only one with advanced CNC certification or NDT knowledge, your production line can stall when they’re absent. Encouraging cross-training not only fills coverage gaps but also expands staff engagement.
Skill matrix and role requirements
Role/Task | Required Skill | Hours | Backup Staff |
---|---|---|---|
Composite layup | Advanced composite licence | 25–30 (peak) | Sarah, James |
Avionics assembly | Electronics/avionics qualification | 20–25 | (Needs cross-training) |
CNC machining | CNC programming & safety induction | 30–35 | Gary, Anita |
NDT (non-destructive) | NDT level II | 15–20 | Mary (level I in progress) |
Final inspection | QA / AS9100 familiarity | 10–15 | QA team rotating |
3.3. Keep it fair and clear
Aerospace thrives on detail, so random rosters betray that principle. Staff appreciate equitable, reasoned scheduling, especially for overnights or weekends. If your approach is transparent, trust grows, a priceless commodity in a tight-knit SME environment.
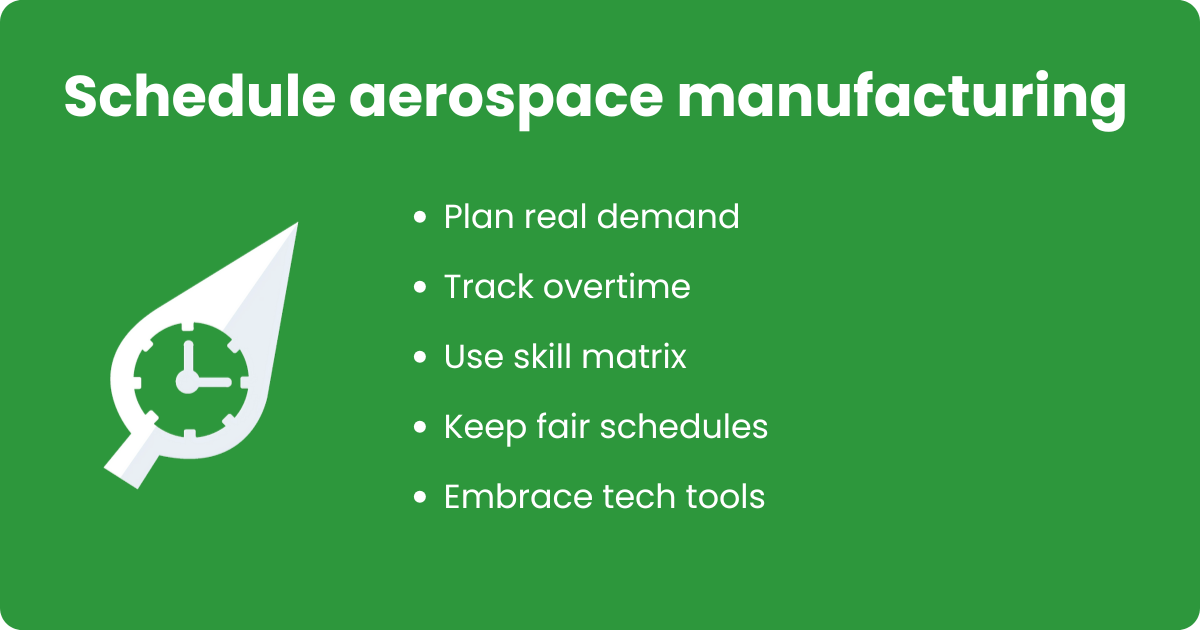
4. Spreadsheets or smart tools?
4.1. Why manual methods fail
Plain spreadsheets rarely integrate compliance checks or live skill validations. One mis-key can seat an unapproved operator on advanced tasks. If your goal is cutting admin duplication and guaranteeing correct placements, a dynamic platform is a must.
4.2. What smaller firms need
- Certification checks: Auto-block tasks for unlicensed staff.
- Labour compliance: Award interpretation for Aussie regulations.
- Overtime watch: Real-time budget notifications to contain cost surges.
- Cloud/mobile: A time clock tool or RosterElf interface for swift roster clarity.
5. Your RosterElf roadmap
5.1. Define specific aims
Pick top scheduling problems—repeated overtime, late deliveries—and translate them into measurable goals (e.g. slash OT by 10%). This focus helps you judge improvements after adopting new methods.
5.2. Map skills, spot gaps
A thorough skill register in a workforce management system unveils who’s truly licensed for advanced tasks. Pairing that with a staff-availability template reveals coverage holes or single-expert stations you must bolster.
5.3. Forecast before firefighting
- Check pipelines: If a surge looms, arrange staff in advance.
- Stagger maintenance: Schedule machine upkeep during non-peak hours.
- Reassign or train: Use team-building sessions or cross-training if certain lines are understaffed.
5.4. Merge compliance and speed
Besides efficiency, aerospace demands legal rest hours and proper skill usage. Systems offering skill-based shift allocation along with leave management coverage spare you from labour-law or licensing blunders.
5.5. Communicate weekly, update daily
Push notifications help, but quick stand-ups let leaders spotlight supply or design changes immediately. Many integrate rosters with time-and-attendance checks for real-time insight on staff availability.
5.6. Embrace change, fine-tune often
Aerospace lines can pivot overnight if parts or designs change. By reviewing rosters daily, you can quickly reassign staff as needed. Some shops pilot a free roster approach alongside traditional methods to confirm improvements in coverage and cost control.
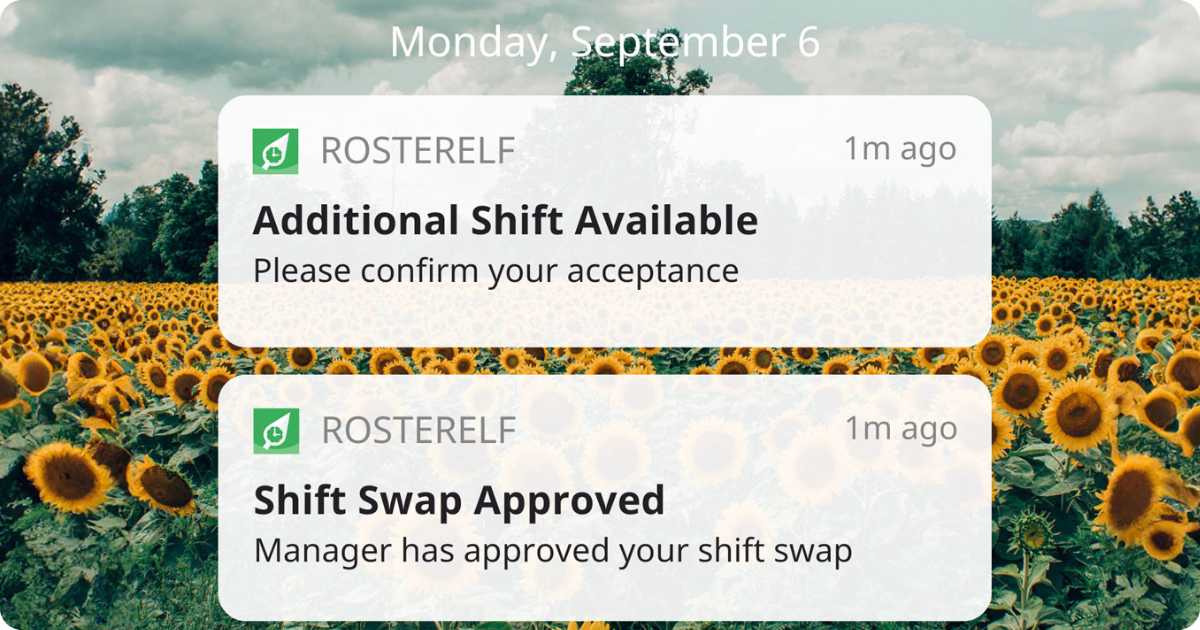
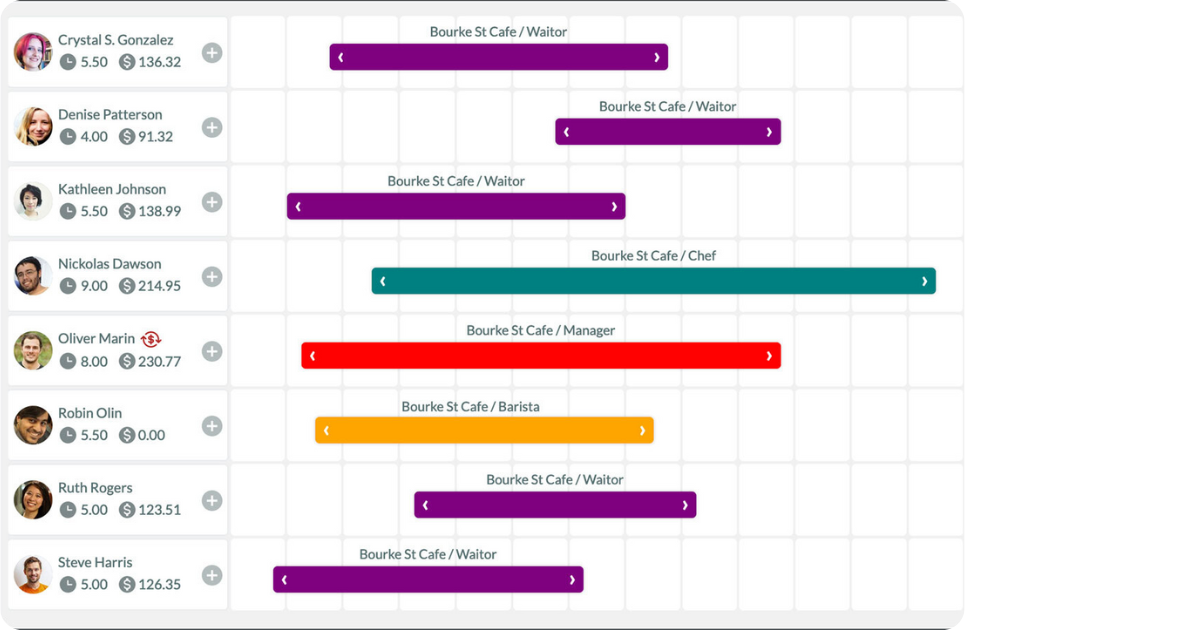
6. Stories and wins you’ll love
6.1. The 20-staff turnaround
A Queensland UAV-part shop relied on a whiteboard, fueling monthly overtime spikes and staff complaints. Transitioning to advanced rostering features with skill-based tasks led to:
- 12% less overtime in three months
- Improved on-time deliveries, pleasing prime contractors
- Better staff satisfaction due to clearer rosters
Freed from daily scheduling chaos, managers tackled deeper process refinements, accelerating quality improvements.
6.2. Lessons from cars and kitchens
- Automotive repair: Align mechanics to specific diagnostic skills. Aerospace mimics this by reinforcing accountability for skill usage.
- Food processing: Time staff around perishability windows. For aerospace, integrating scheduling with payroll ensures timely staff arrivals, reducing idle time.
Both examples show how organised shift planning lowers error rates and idle labour—key objectives in precision aerospace.
7. Rules, records, and Aussie realities
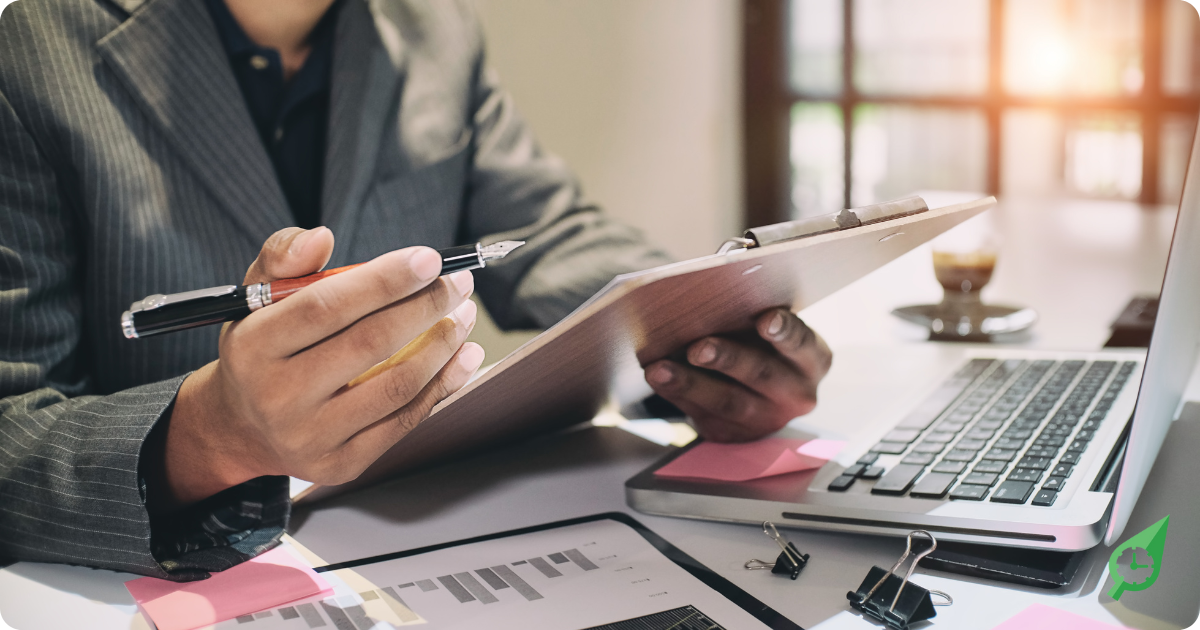
7.1. CASA, AS9100, and market shifts
The Civil Aviation Safety Authority mandates licensing, while AS9100 guidelines frame quality assurance. Deloitte’s supplier analysis shows scheduling is linked to consistent deliveries. Negligent rosters can threaten compliance and reliability.
7.2. Fair work for steady peace
The Fair Work Ombudsman outlines standards for hours, breaks, and overtime in Australia. Some shops handle union pacts with rotation of weekends or shifts. Using automated compliance checks assures staff that working conditions are law-abiding and fair.
7.3. Fatigue? Halt it early
Advanced tasks such as welding or flight-control rigging demand unwavering focus. Overstretching staff kills quality. A time clock tool monitoring hours can alert managers when staff approach unsafe thresholds, preventing costly errors.
7.4. Keep tidy audit trails
Paper rosters are easily lost or outdated. A cloud-based system that timestamps every update provides a reliable log for audits. Coupling this with regular team-building or training sessions helps maintain transparency—a critical factor under strict aerospace audits.
8. Measure, improve, repeat
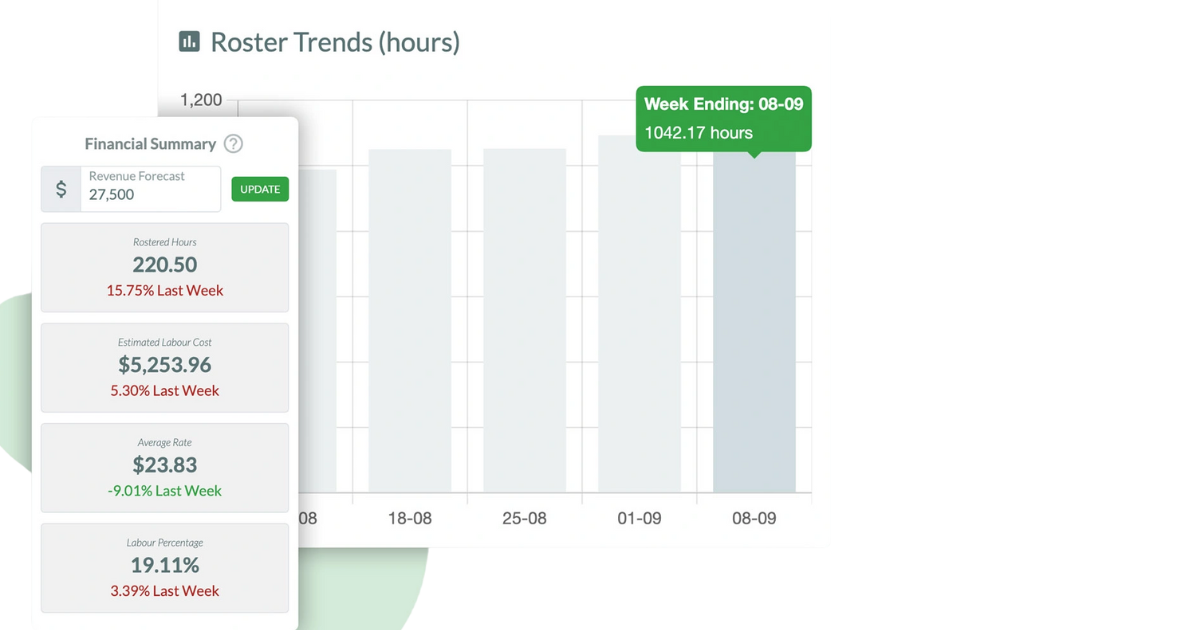
8.1. Track overtime, guard budgets
Frequent checks—weekly or daily—reveal cost overruns early. If production lines consistently exceed planned hours, adjust forecasts or train additional staff. A staff availability template can indicate who might share extra workload.
8.2. Spot gaps, add backups
If managers routinely scramble to cover shifts, it signals staffing gaps. Identify positions with limited coverage and consider cross-training or recruiting additional backup operators.
8.3. Boost flow, slash delays
When every station is appropriately staffed, workflow improves dramatically. Consistent rosters lead to smoother handoffs and more reliable production schedules. Many SMEs use a free roster trial to quantify lead-time gains.
8.4. Listen to operator insights
Technicians on the floor can spot scheduling issues that raw data might miss. Regularly ask for their feedback, then combine it with efficiency metrics to adjust rosters in a balanced way.
9. Conquer real-world obstacles
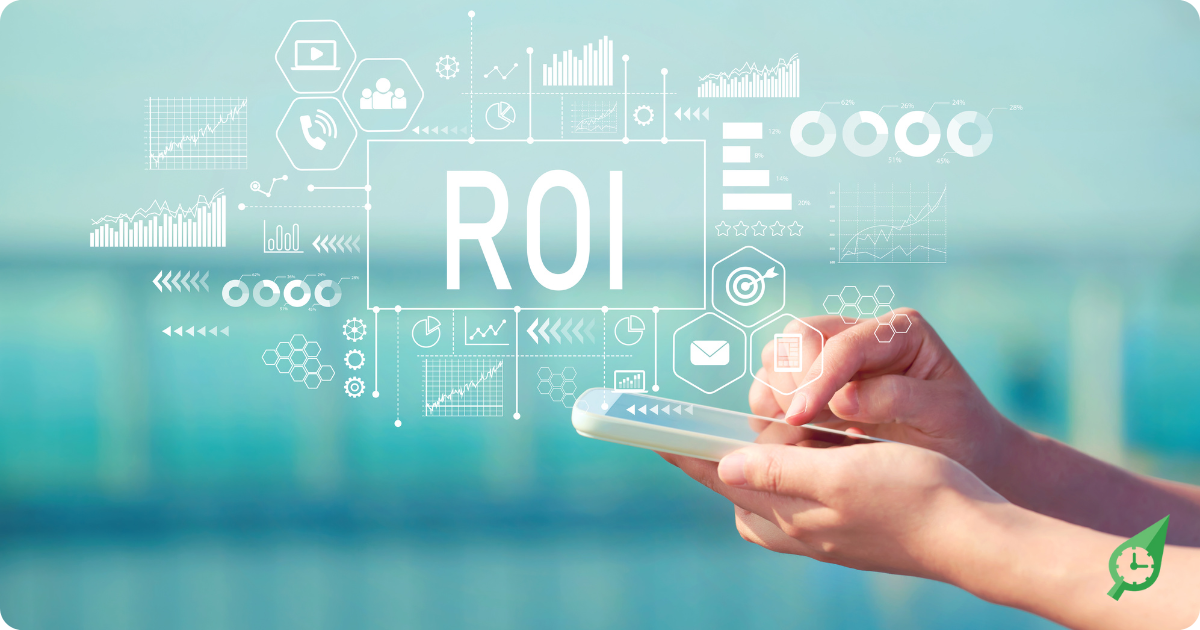
9.1. Proving the ROI
Subscription fees may seem steep, but flawed scheduling costs more in rework and missed opportunities. Many SMEs that adopt comprehensive scheduling software see immediate labour savings that justify the investment.
9.2. Winning over old hands
Seasoned employees might resist new scheduling tools. Emphasise the benefits of consistent rosters, reduced overtime, and tasks matched to their skills. Demonstrate how a skill-based approach can reduce daily chaos and improve morale.
9.3. Adopt without tech pain
Modern cloud solutions like RosterElf require only a web browser and straightforward onboarding—no heavy IT support needed. This ease of adoption helps SMEs scale scheduling improvements rapidly.
9.4. Stay watchful, stay sharp
What works today might falter tomorrow if product lines or staff credentials change. Designate a “roster champion” to update skills and shift assignments, ensuring your system remains agile and accurate.
10. What’s next? AI, wearables, and more
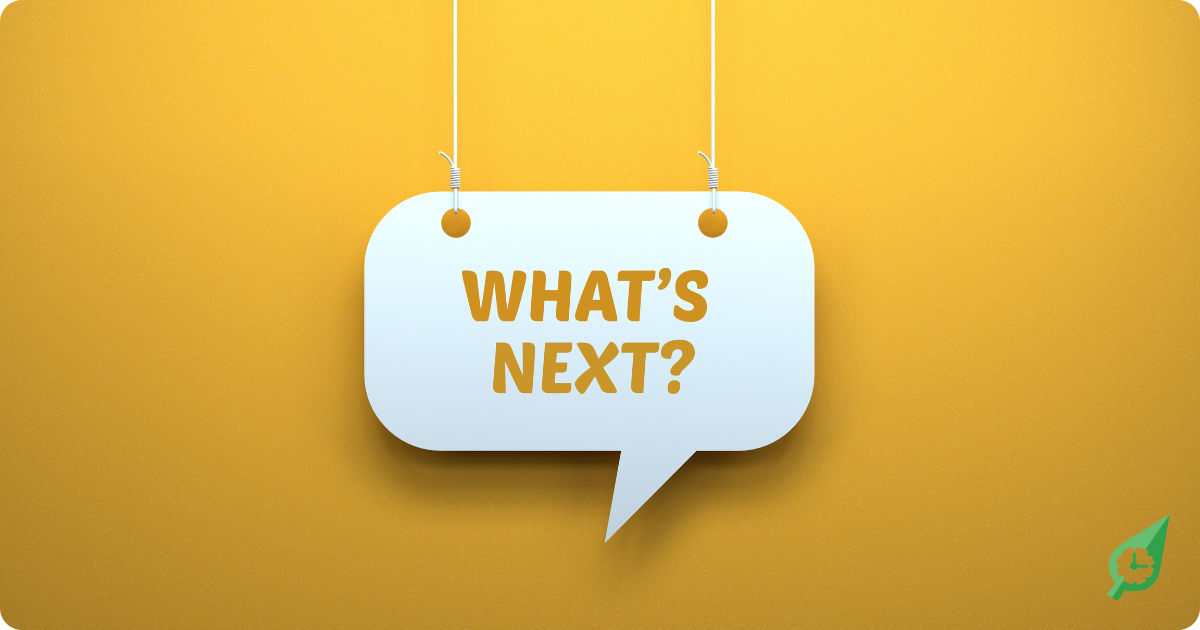
10.1. AI for smaller shops
Large players harness AI scheduling integrated with production logs. SMEs can adopt scaled-down AI tools that review backlogs or design changes. When paired with a mobile time clock, these systems automatically refine planned hours versus actual hours, offering unprecedented flexibility.
10.2. Gear up with wearable safety
Smartwatches or sensor-equipped uniforms can detect fatigue in real time. Although initially cutting-edge, prices drop over time. Trial such technology alongside a RosterElf free trial to see how live health metrics can guide shift reassignments, especially for tasks requiring high concentration.
10.3. Skill-sharing across sites
In regional clusters, one aerospace shop might have idle capacity while another is overloaded. Scheduling software that logs skill sets across multiple sites allows for inter-company staff lending. Auto-shift swaps across sites can quickly resolve urgent coverage issues, enhancing local competitiveness.
10.4. Wellbeing as a winning edge
Attracting and retaining skilled aerospace talent requires more than competitive pay. Ensuring consistent rosters and honoring mandated rest periods can differentiate your SMB. Employees also value no-cost HR tools that simplify onboarding and training, bolstering your brand as an employer of choice.
11. Why this edge matters
Mastering aerospace manufacturing shift scheduling with RosterElf goes beyond reducing administrative burdens. In an industry where precision is paramount, scheduling can determine daily productivity and compliance. One overlooked skill check or forced overtime can erode both morale and client trust.
By integrating skill-based rosters, live updates, and compliance controls, you meet the exacting standards of aerospace. Employees benefit from consistent shifts, managers avoid last-minute crises, and clients receive reliable service. For small Australian operators, these gains provide a significant competitive edge.
If you remain uncertain about labour laws or union specifics, consult HR experts. When combined with a dedicated scheduling platform, this assurance helps maintain agility in an industry that demands unwavering commitment.
12. Reinvent shifts with RosterElf
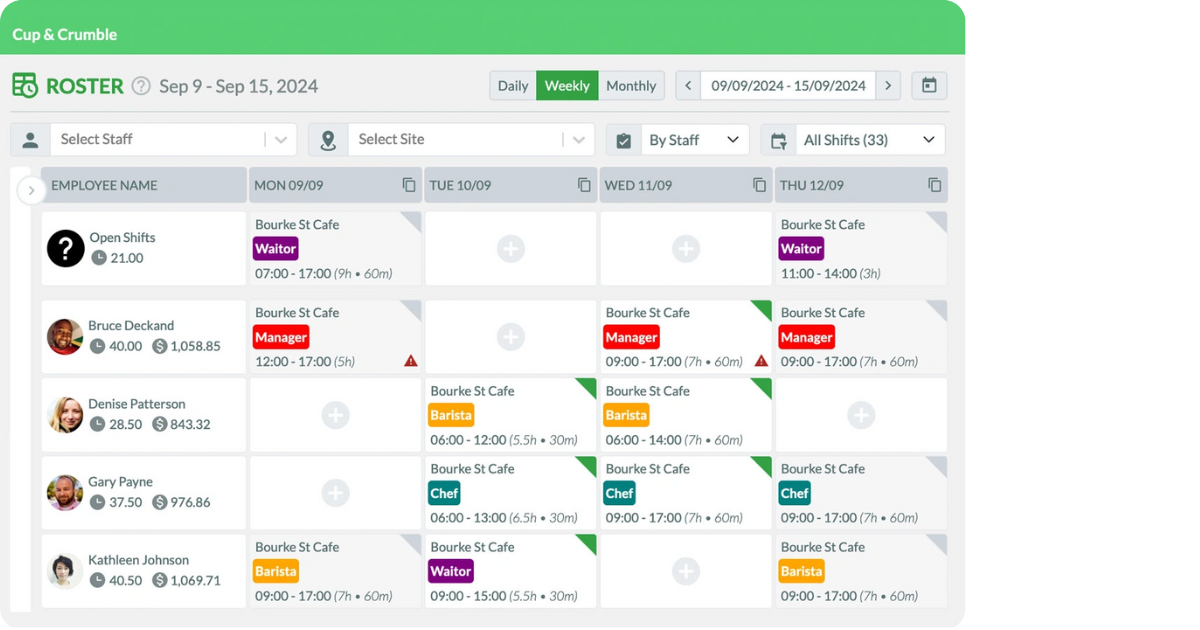
If you’re aiming to modernise your aerospace production, RosterElf blends compliance, skill oversight, and ease of use into one comprehensive scheduling suite. Our platform:
- Matches tasks to the right expertise: Prevents idle hours or misallocations by ensuring each shift is assigned based on verified skills.
- Keeps labour on budget: Provides real-time alerts if labour costs spike, promoting transparency and accountability.
- Offers quick roster updates: Access our platform from anywhere—ready for a free trial to see immediate improvements in your scheduling.
- Respects local labour codes: Through award interpretation and payroll alignment, every shift meets Australian standards.
Book a short demo to discover how refined scheduling frees admin hours, manages labour costs, and adapts to sudden changes. Choosing a top-tier scheduling method anchors daily stability and reflects the precision prized in Australia’s aerospace arena.
Disclaimer: This article reflects professional observations within Australian aerospace. It does not replace official legal, financial, or compliance advice. Please consult qualified experts for specific concerns.
10. Finish line: empowering your SMB beyond underperformance
In smaller operations, staff underperformance can do more than dent daily numbers: it can unravel your team’s unity and stall growth. While large organisations may absorb occasional slack, SMBs feel every deficit in engagement. Overcoming that fate involves addressing five overlapping roots—management disengagement, no staff growth, limited rewards, personal burdens, and low motivation—as a cohesive strategy.
- Stay hands-on: Frequent presence, open communication, and immediate praise keep teams motivated.
- Champion growth: Cross-training, micro-promotions, or skill-based projects provide a clear path for development.
- Reward openly: Transparent and fair incentives help staff feel genuinely appreciated.
- Support personal struggles: Flexible rosters or additional leave options can help maintain morale during challenging times.
- Mix up motivation: Recognise that some staff thrive on recognition, others on variety, and still others on autonomy.
By integrating these solutions, staff underperformance becomes a manageable issue rather than a chronic challenge. Combine these initiatives with clear scheduling—through RosterElf—to eliminate logistical headaches that often sap morale and hinder productivity. With empathetic leadership, ongoing skill development, genuine incentives, and well-planned shifts, your SMB can sustain strong momentum without frequent performance dips.